Battery Production Solutions by LEWA: Innovative, Efficient, and Sustainable Manufacturing
Crucial Role of Rechargeable Battery Production in Electric Mobility and Renewable Energy Storage for Sustainability
To ensure the quality and specific characteristics of a battery, such as capacity or charging speed, active materials and additives are used in specific ratios depending on the intended application. Special chemicals play an important role in the extraction of raw materials from primary and secondary sources.
With LEWA and NIKKISO products, we support our customers in specialized plant construction or directly in production areas to meet the high demands of end products. Robust pumps ensure high productivity, intelligent drive concepts enable flexible use over a wide range of production capacities, and the high repeatability of dosing systems ensures precise adherence to formulations.
With pumps and systems from LEWA
Explore Diverse Battery Production Applications with LEWA: Tailored Solutions for Every Need
Discover LEWA's Comprehensive Range of Battery Production Applications: Customized Solutions for Enhanced Efficiency and Performance
Raw Materials
Every battery cell requires a specific mix of special raw materials for its functionality and application. These include rare earth elements, lithium, manganese, and cobalt, found in hard rock or dissolved in underground saline water sources. Through dissolution and precipitation processes using special chemicals, the desired materials are extracted and purified before being processed into the various components of a battery…
More on this topicChemical / Component Manufacturing
Various functional components and specially mixed fluids together form a battery cell. In addition to the housing and cover, the main components include the anode, cathode, separator, and electrolyte. Each component has its own manufacturing process, with the properties of some being influenced by the proportions of the involved raw materials.
More on this topicBattery Assembly
In the assembly step, the required components are combined into battery cells and filled with electrolyte. Depending on the desired size and application, multiple cells are combined into a single battery module, and these modules are further assembled into a battery pack. After final sealing and the application of gaskets, various tests (e.g., leak testing, heat development, performance) and controlled charging (formation) are…
More on this topicBattery Recycling
To sustainably manage limited resources like lithium and cobalt, not only from primary sources but also from production scrap and end-of-life batteries, recycling processes are becoming increasingly important. After the battery modules are discharged for safety reasons, they are dismantled into subcomponents. The subsequent recycling steps include mechanical recycling to recover electrolyte, screws, cables, and plastic from…
More on this topicComprehensive Guide to Pumps Utilized in Battery Production
Explore the Full Range of High-Performance Pumps Essential for Efficient Battery Production
Product Name | Product Image | Technology | Flow Rate | Discharge Pressure | Purpose | |
---|---|---|---|---|---|---|
LEWA triplex®: Compact Process Pumps for High-Pressure Applications | ![]() | Technology: Hydraulically actuated process diaphragm pump in monoblock design | 19 m³/h per pump head | 1.200 bar | Hard Rock Mining | To the Pump |
LEWA ecoflow® Packed Plunger Metering Pumps | ![]() | Technology: Packed plunger metering pump | 9 m³/h per pump head | 500 bar | Direct Lithium Extraction (DLE) | To the Pump |
NIKKISO NON-SEAL canned motor pump | ![]() | Technology: Canned motor pump | 1000 m³/h | 20 MPa | Pumps for NMP Handling | To the Pump |
LEWA triplex®: Compact Process Pumps for High-Pressure Applications | ![]() | Technology: Hydraulically actuated process diaphragm pump in monoblock design | 180 m³/h per pump | 1200 bar | Electrolyte Production | To the Pump |
LEWA ecoflow® Diaphragm Metering Pump | ![]() | Technology: Hydraulic actuated diaphragm metering pump | 19 m³/h per pump head | 1200 bar | Separator Manufacturing | To the Pump |
LEWA ecoflow®: Process Pumps for High-Pressure Applications | ![]() | Technology: Hydraulically actuated process diaphragm pump in modular construction | 19 m³/h per pump head | 1200 bar | Processing of Black Mass | To the Pump |
Raw Materials
Extraction of Lithium for Battery Production from Primary Sources
Lithium is naturally found in various types of rock, as well as dissolved in underground saline water deposits. Using appropriate dissolution and extraction processes, it can be separated, purified, and converted into lithium carbonate or lithium hydroxide for transport to further processing steps.
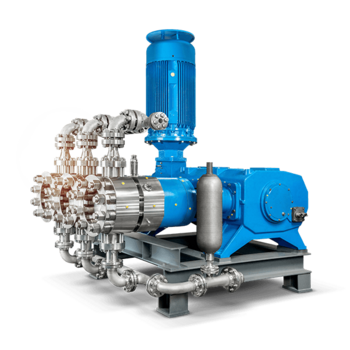
Hard Rock Mining
Sulfuric acid and caustic soda are primarily used in processing crushed lithium-bearing minerals such as spodumene and petalite. After acid leaching, several filtration and precipitation steps follow. Our robust products play a crucial role in ensuring the smooth operation of these interconnected processes by accurately dosing the fluids. They withstand aggressive environmental conditions with long maintenance intervals.
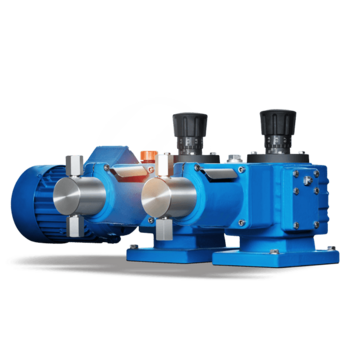
Direct Lithium Extraction (DLE)
Analyses of underground water sources used for geothermal energy sometimes reveal significant concentrations of lithium. Typically, geothermal water is re-injected into the reservoirs after its thermal energy is utilized. However, in the DLE process, various methods are employed as an intermediate step to separate the desired lithium ions from the brine. Our pumps can precisely handle not only the brine but also auxiliary substances like solvents or acids used for regenerating ion exchangers.
With pumps and systems from LEWA
Application areas with LEWA pumps and systems
Explore the Full Range of High-Performance Pumps Essential for Efficient Battery Production
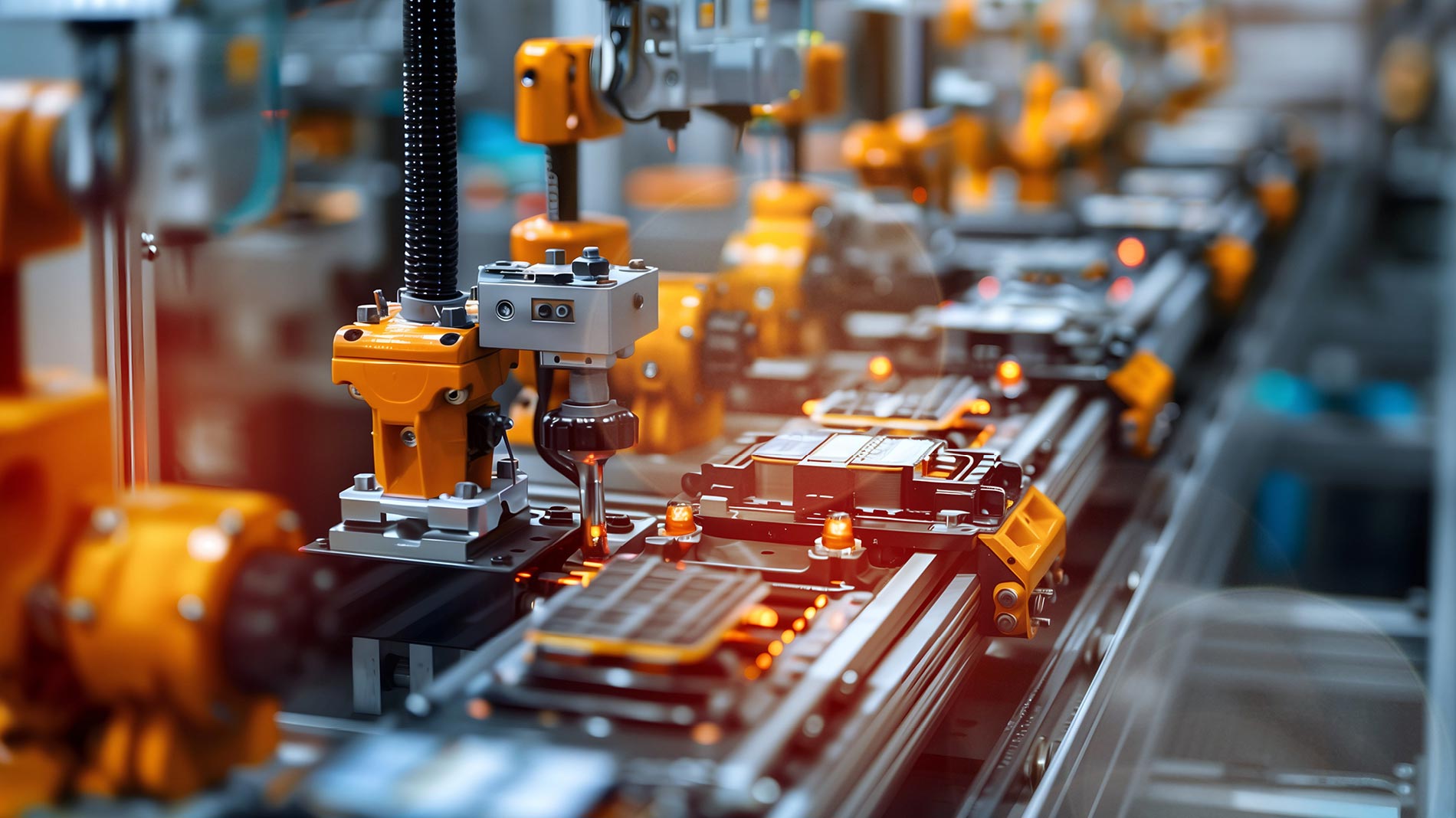
Chemical / Component Manufacturing
A battery cell is composed of various functional components and specially blended fluids. The primary elements include the anode, cathode, separator, and electrolyte, in addition to the housing and cover. Each component undergoes its unique manufacturing process, and the characteristics of certain parts are affected by the ratios of the raw materials used.
More on this topic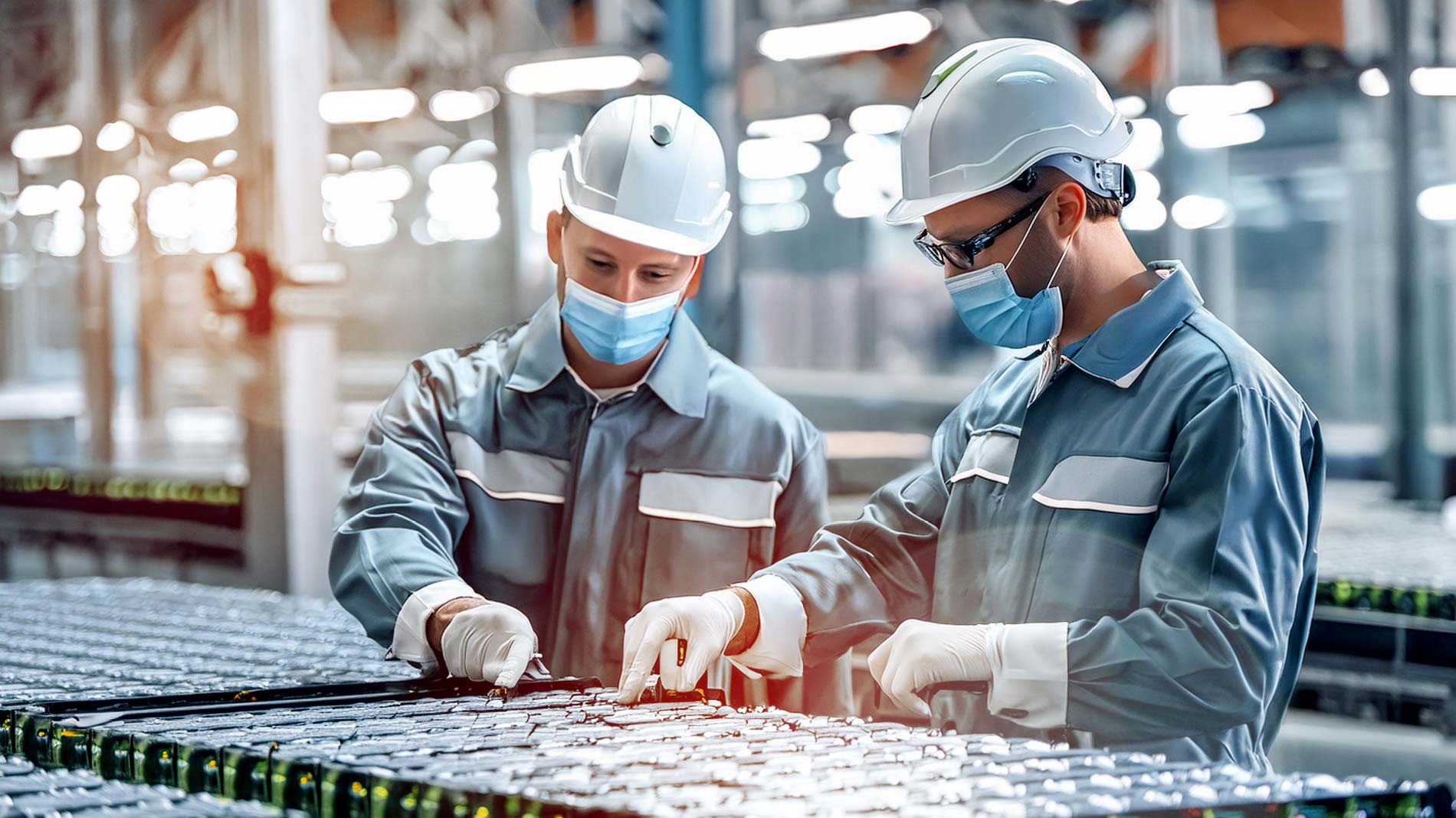
Battery Assembly
During the assembly phase, the necessary components are brought together to form battery cells, which are then filled with electrolyte. Based on the intended size and use, several cells can be combined into a battery module, and these modules are subsequently assembled into a battery pack. Following the final sealing and application of gaskets, a series of tests (such as leak testing, heat development, and performance) and controlled charging (formation) are performed.
More on this topic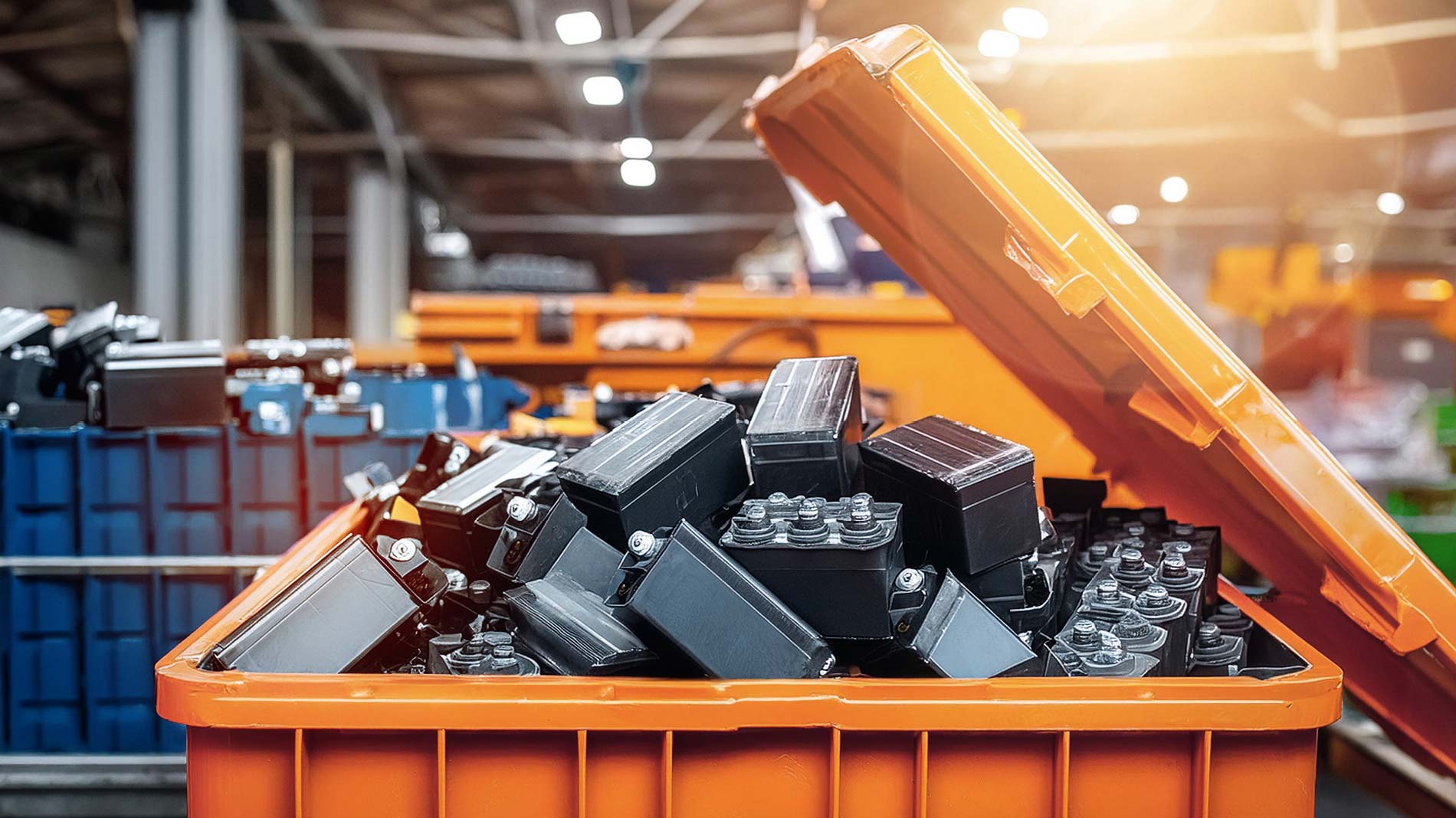
Battery Recycling
To sustainably manage limited resources like lithium and cobalt from primary sources, production scrap, and end-of-life batteries, recycling is increasingly important. After safely discharging battery modules, they are dismantled into subcomponents. Recycling stages include mechanical recycling to retrieve electrolyte, screws, cables, and plastic from shredded casings. Pyrometallurgy generates alloys and slags containing copper, cobalt, nickel, and lithium. Hydrometallurgy, or wet chemical processes, recover valuable metals through acid treatment of finely ground active materials, followed by precipitation and extraction reactions.
More on this topicChemical / Component Manufacturing for Battery Production
Production of Electrolyte and Other Battery Cell Components
To maintain the long-term consistency of a battery module's properties and prevent malfunctions such as short circuits or critical temperature increases, high-purity chemicals and active materials are used. Depending on the application, the mixtures of the electrolyte or electrode slurry vary. Thus, in addition to the quality of raw materials, adhering to the correct formulation is of critical importance.
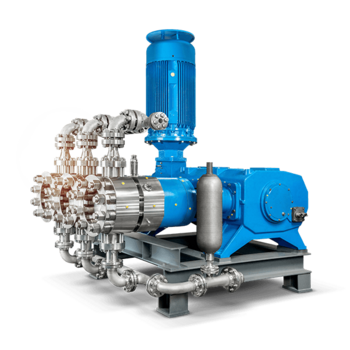
Electrolyte Production
In electrolyte solutions, the lithium-containing conductive salt is accompanied by solvents such as ethylene carbonate (EC) and dimethyl carbonate (DMC). While DMC is derived from EC, ethylene oxide and CO2 are the starting materials for the reaction to EC. These and other challenging fluids involved in the process can be safely and reliably handled with hermetically sealed LEWA pumps. Their inherent dosing accuracy ensures dependable process management.
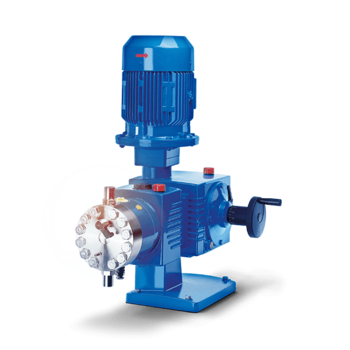
Separator Manufacturing
Between the anode and cathode, a porous separator material is embedded to electrically isolate the two electrode areas while still allowing ion transport. In the wet process, mineral or white oil is dosed into the melt for the separator film during the extrusion process. This oil later forms finely distributed micropores when it is washed out with a suitable solvent. For homogeneous distribution, it is important to match and maintain the injected oil's proportion to the current extruder throughput. With wide dosing ranges and precise control, we enable this and facilitate flexible production.
With pumps and systems from LEWA
Application areas with LEWA pumps and systems
Explore the Full Range of High-Performance Pumps Essential for Efficient Battery Production
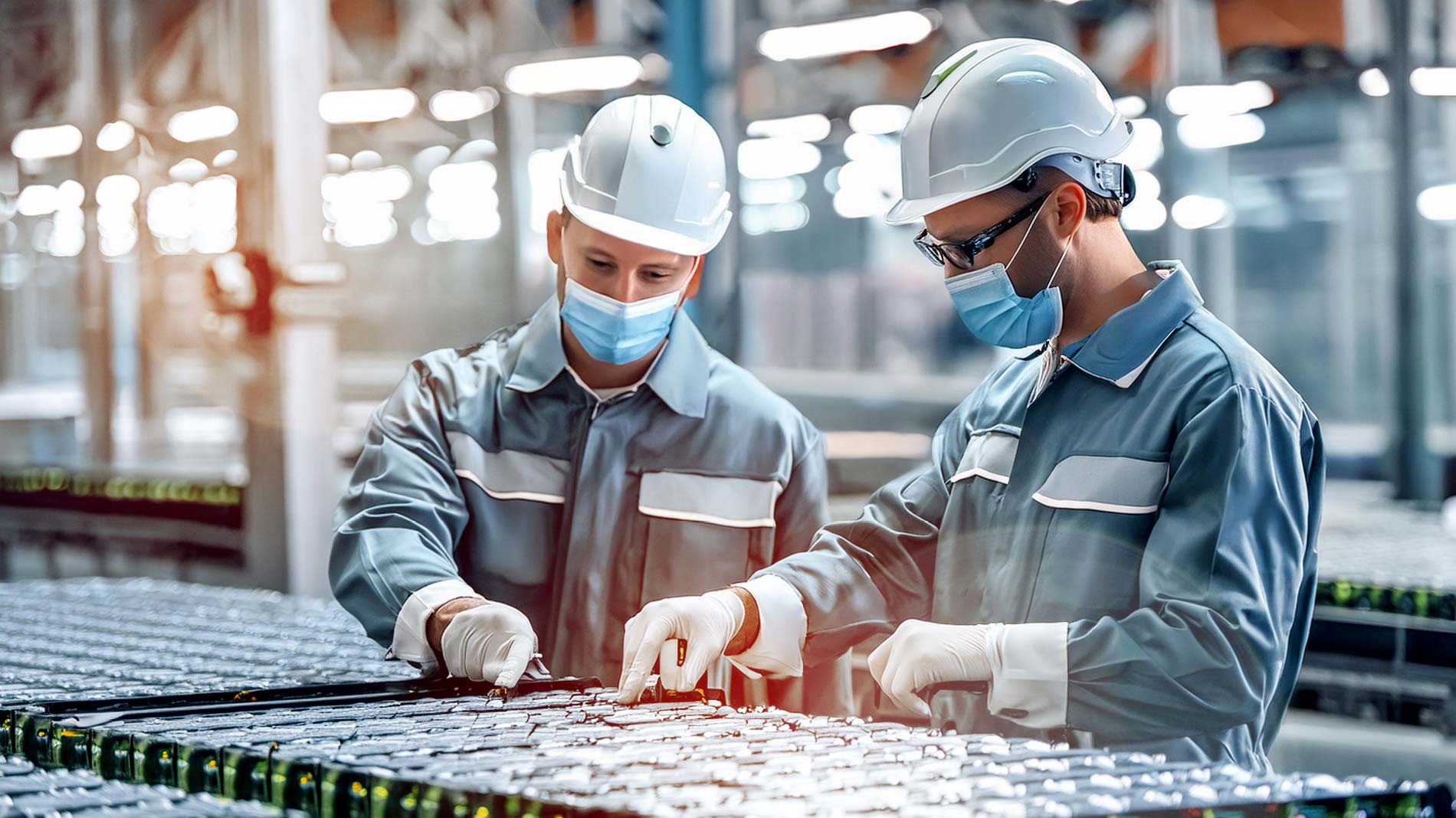
Battery Assembly
During the assembly phase, the necessary components are brought together to form battery cells, which are then filled with electrolyte. Based on the intended size and use, several cells can be combined into a battery module, and these modules are subsequently assembled into a battery pack. Following the final sealing and application of gaskets, a series of tests (such as leak testing, heat development, and performance) and controlled charging (formation) are performed.
More on this topic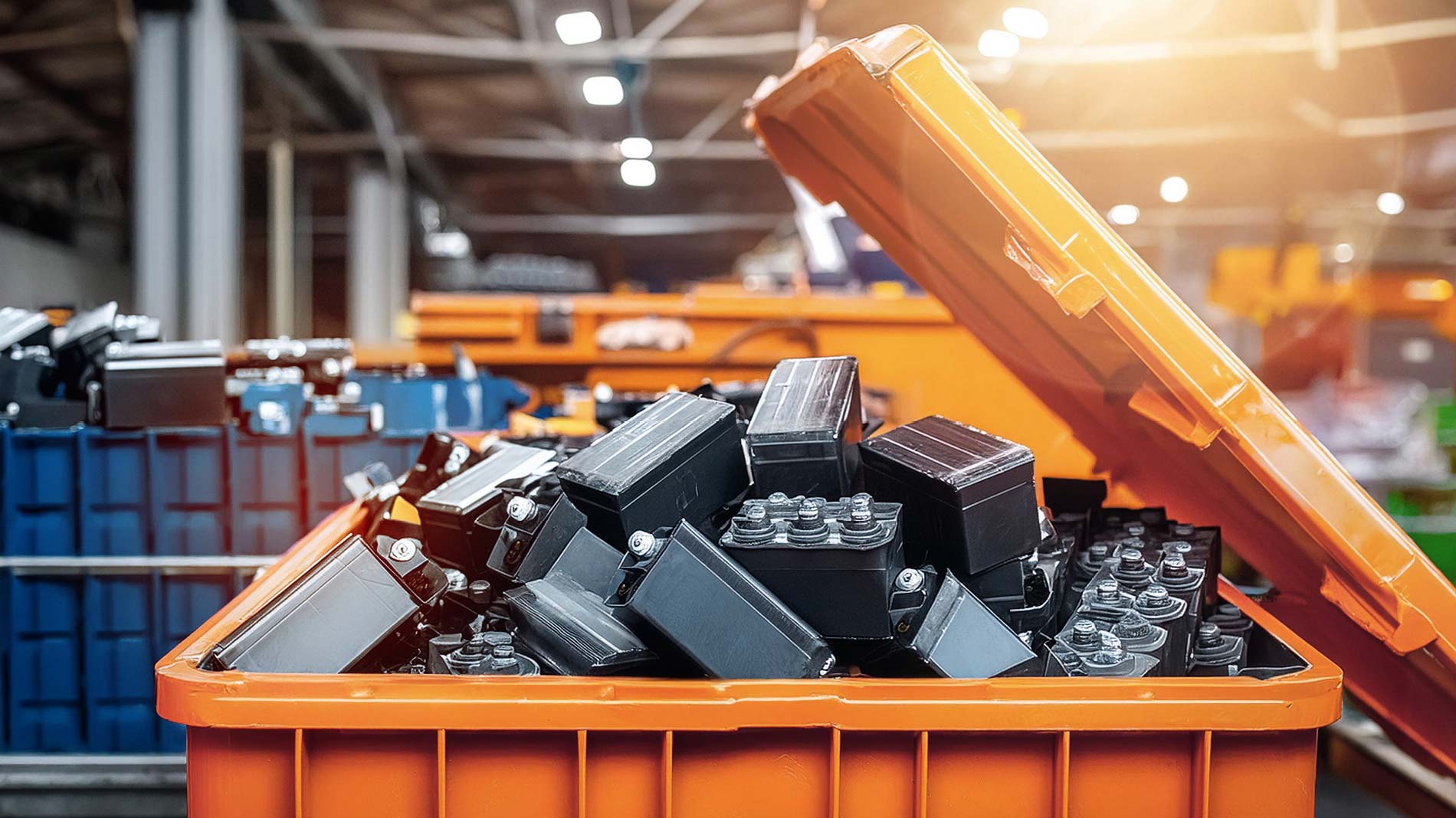
Battery Recycling
To sustainably manage limited resources like lithium and cobalt from primary sources, production scrap, and end-of-life batteries, recycling is increasingly important. After safely discharging battery modules, they are dismantled into subcomponents. Recycling stages include mechanical recycling to retrieve electrolyte, screws, cables, and plastic from shredded casings. Pyrometallurgy generates alloys and slags containing copper, cobalt, nickel, and lithium. Hydrometallurgy, or wet chemical processes, recover valuable metals through acid treatment of finely ground active materials, followed by precipitation and extraction reactions.
More on this topic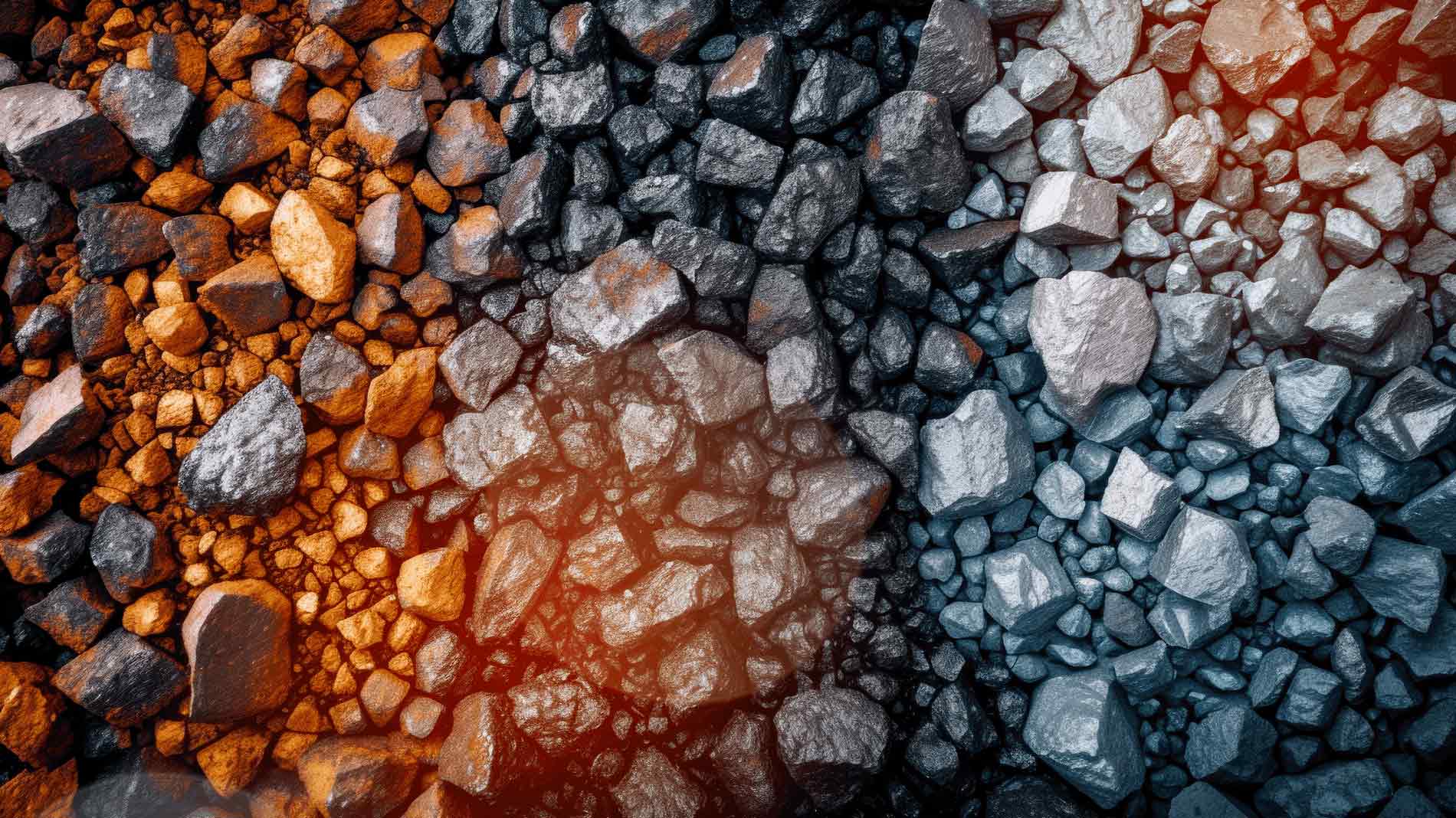
Raw Materials
Each battery cell necessitates a unique blend of specialized raw materials to ensure its functionality and suitability for its intended application. These materials encompass rare earth elements, lithium, manganese, and cobalt, which are either mined from hard rock or extracted from underground saline water deposits. Using specific chemicals, these materials undergo dissolution and precipitation processes to be extracted and purified. Subsequently, they are processed into the various components of a battery cell during the following production stages.
More on this topicBattery Assembly
Disassembly of Battery Modules at End-of-Life (EOL) and Recovery of Valuable Materials
In the assembly step, the required components are combined into battery cells and filled with electrolyte. In the production of some of these components, the solvent NMP (N-methyl-2-pyrrolidone) plays a crucial role. It ensures that key fluids are dispensable and can be removed in an evaporation step after successful use. To minimize costs, NMP is collected, condensed, and reused after purification.
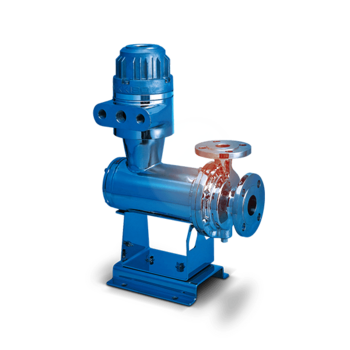
Pumps for NMP Handling
Whether it's preparing slurries for cathode production, coating separator fabric, or general conveyance in the regeneration cycle of a production facility, NMP must be safely handled at many points along the battery manufacturing value chain. Due to its inhalation toxicity, leak-proof conveyance systems are recommended. NIKKISO canned motor pumps are specifically designed for handling critical and hazardous media.
With pumps and systems from LEWA
Application areas with LEWA pumps and systems
Explore the Full Range of High-Performance Pumps Essential for Efficient Battery Production
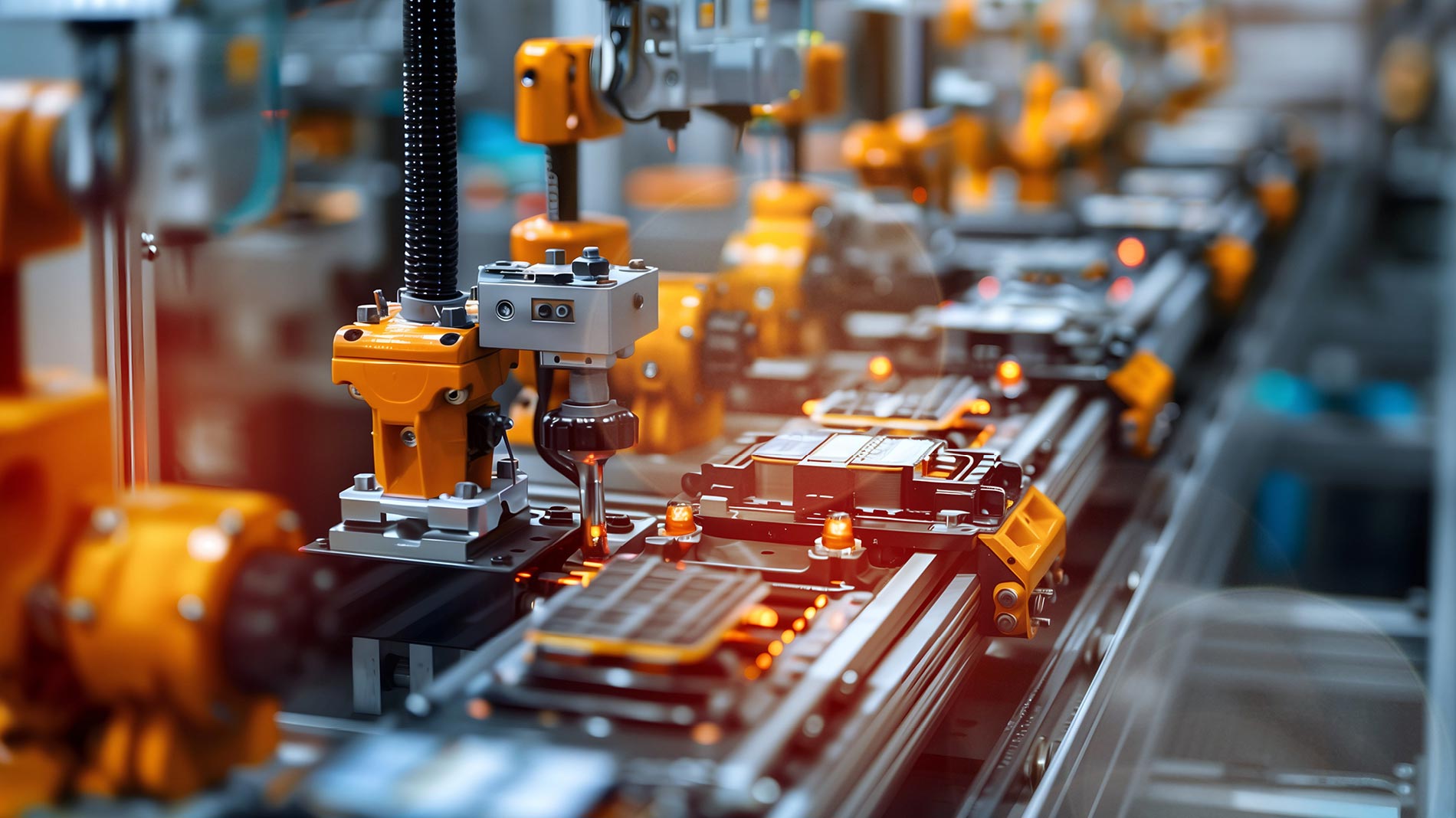
Chemical / Component Manufacturing
A battery cell is composed of various functional components and specially blended fluids. The primary elements include the anode, cathode, separator, and electrolyte, in addition to the housing and cover. Each component undergoes its unique manufacturing process, and the characteristics of certain parts are affected by the ratios of the raw materials used.
More on this topic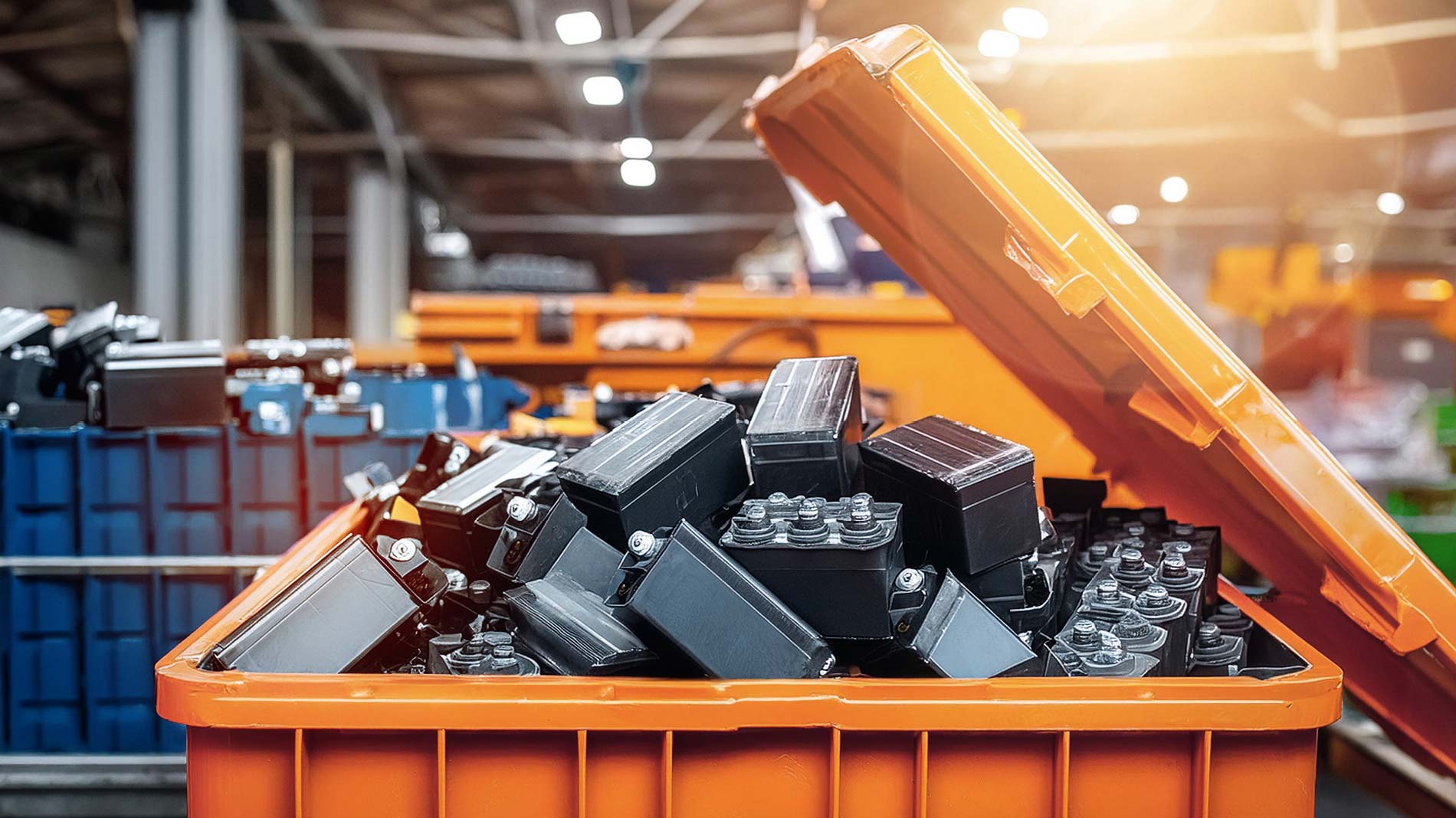
Battery Recycling
To sustainably manage limited resources like lithium and cobalt from primary sources, production scrap, and end-of-life batteries, recycling is increasingly important. After safely discharging battery modules, they are dismantled into subcomponents. Recycling stages include mechanical recycling to retrieve electrolyte, screws, cables, and plastic from shredded casings. Pyrometallurgy generates alloys and slags containing copper, cobalt, nickel, and lithium. Hydrometallurgy, or wet chemical processes, recover valuable metals through acid treatment of finely ground active materials, followed by precipitation and extraction reactions.
More on this topic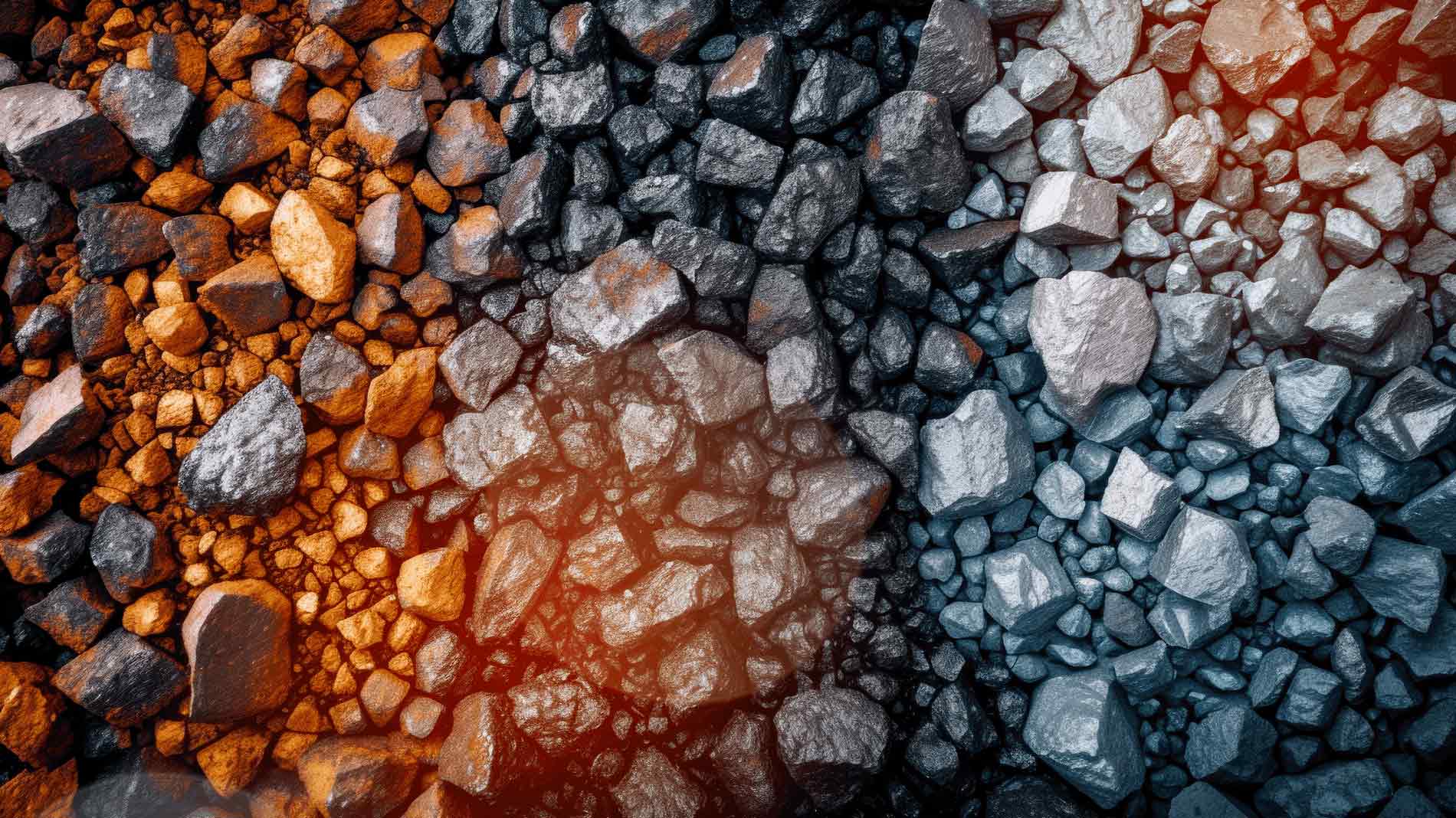
Raw Materials
Each battery cell necessitates a unique blend of specialized raw materials to ensure its functionality and suitability for its intended application. These materials encompass rare earth elements, lithium, manganese, and cobalt, which are either mined from hard rock or extracted from underground saline water deposits. Using specific chemicals, these materials undergo dissolution and precipitation processes to be extracted and purified. Subsequently, they are processed into the various components of a battery cell during the following production stages.
More on this topicBattery Recycling
Recovery of Valuable Raw Materials from Black Mass
When battery modules no longer provide sufficient performance for use as stationary storage ("second life") or are production scrap, important raw materials such as cobalt, nickel, manganese, and lithium can be recovered through recycling. In the future, this will become an increasingly important supplement to primary sources. In addition to mechanical recycling and pyrolysis, wet chemical processes (hydrometallurgy) are also used.
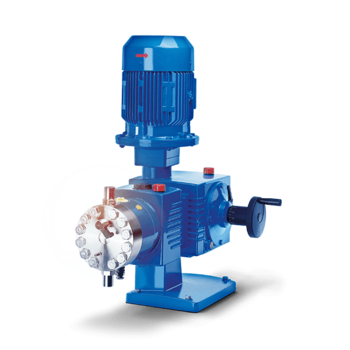
Processing of Black Mass
When black mass, resulting from the shredding of used batteries, is separated from other components, it may be pre-cleaned through pyrolysis (removal of binders and fluorine-containing elements). Afterward, hydrometallurgical processes allow for the clean extraction of the desired metals. Similar to hard rock mining, leaching with specific chemicals precedes the precipitation steps. Pumps with high corrosion resistance and precise dosing ensure smooth operation in this process.
With pumps and systems from LEWA
Application areas with LEWA pumps and systems
Explore the Full Range of High-Performance Pumps Essential for Efficient Battery Production
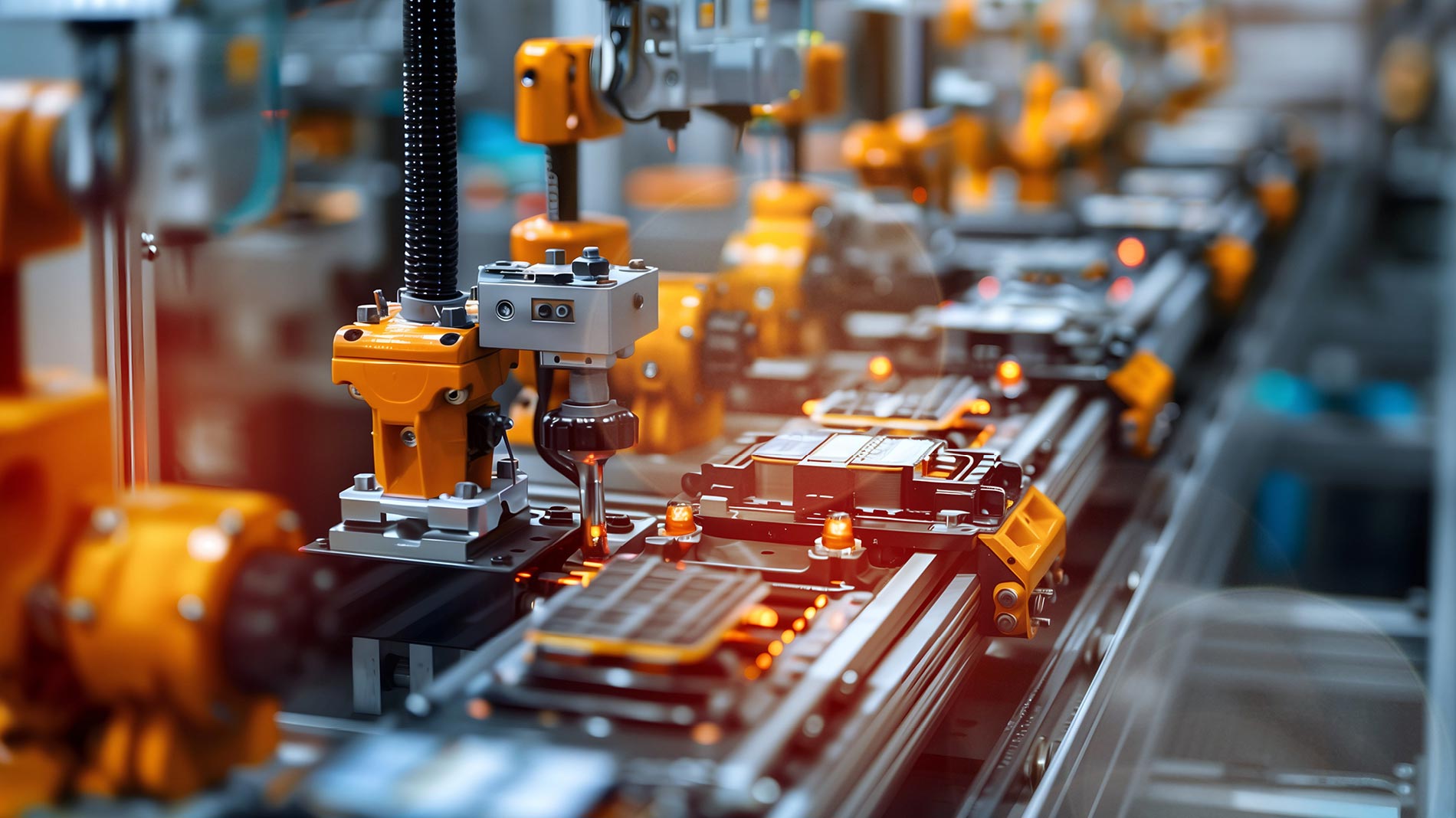
Chemical / Component Manufacturing
A battery cell is composed of various functional components and specially blended fluids. The primary elements include the anode, cathode, separator, and electrolyte, in addition to the housing and cover. Each component undergoes its unique manufacturing process, and the characteristics of certain parts are affected by the ratios of the raw materials used.
More on this topic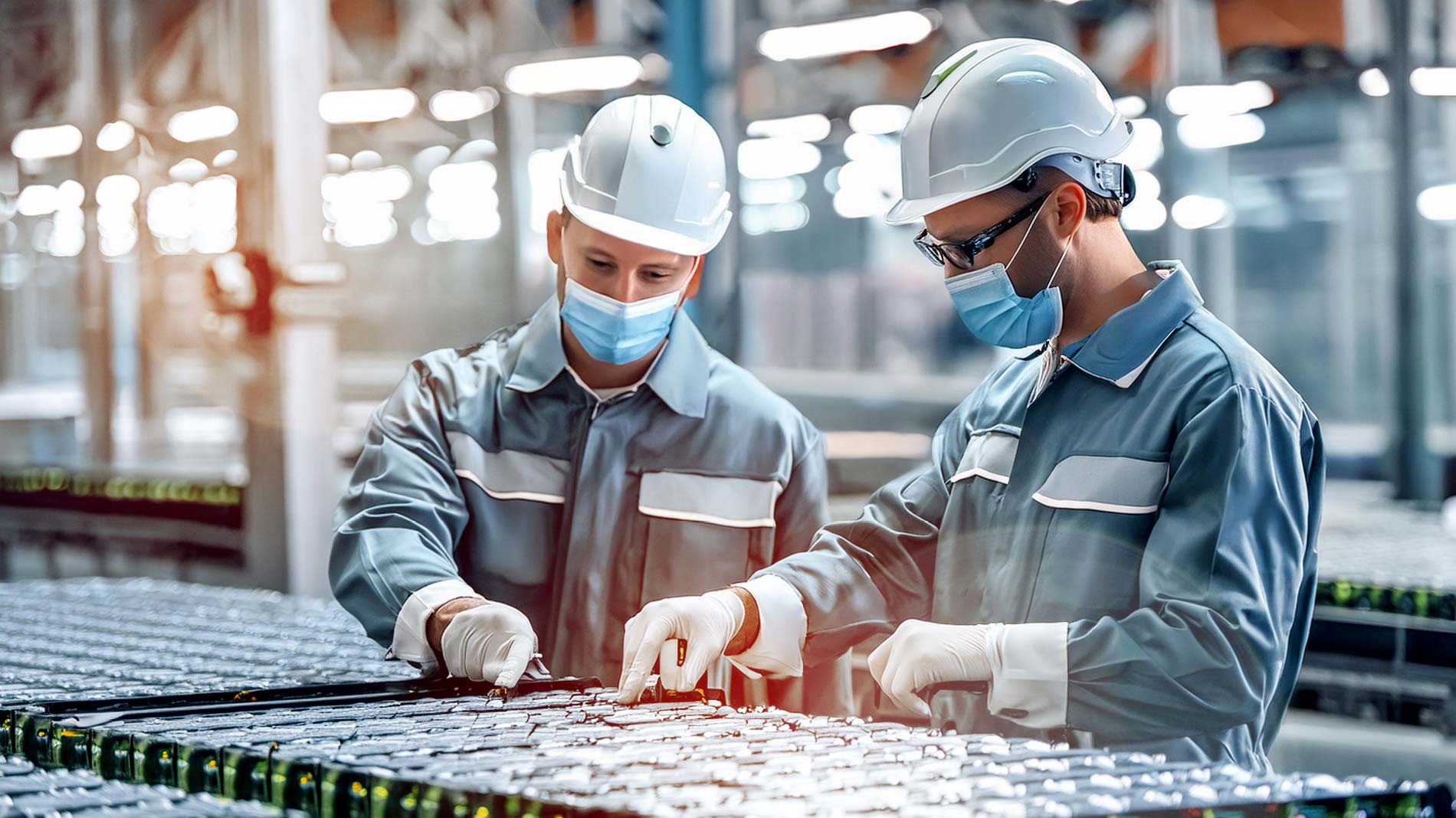
Battery Assembly
During the assembly phase, the necessary components are brought together to form battery cells, which are then filled with electrolyte. Based on the intended size and use, several cells can be combined into a battery module, and these modules are subsequently assembled into a battery pack. Following the final sealing and application of gaskets, a series of tests (such as leak testing, heat development, and performance) and controlled charging (formation) are performed.
More on this topic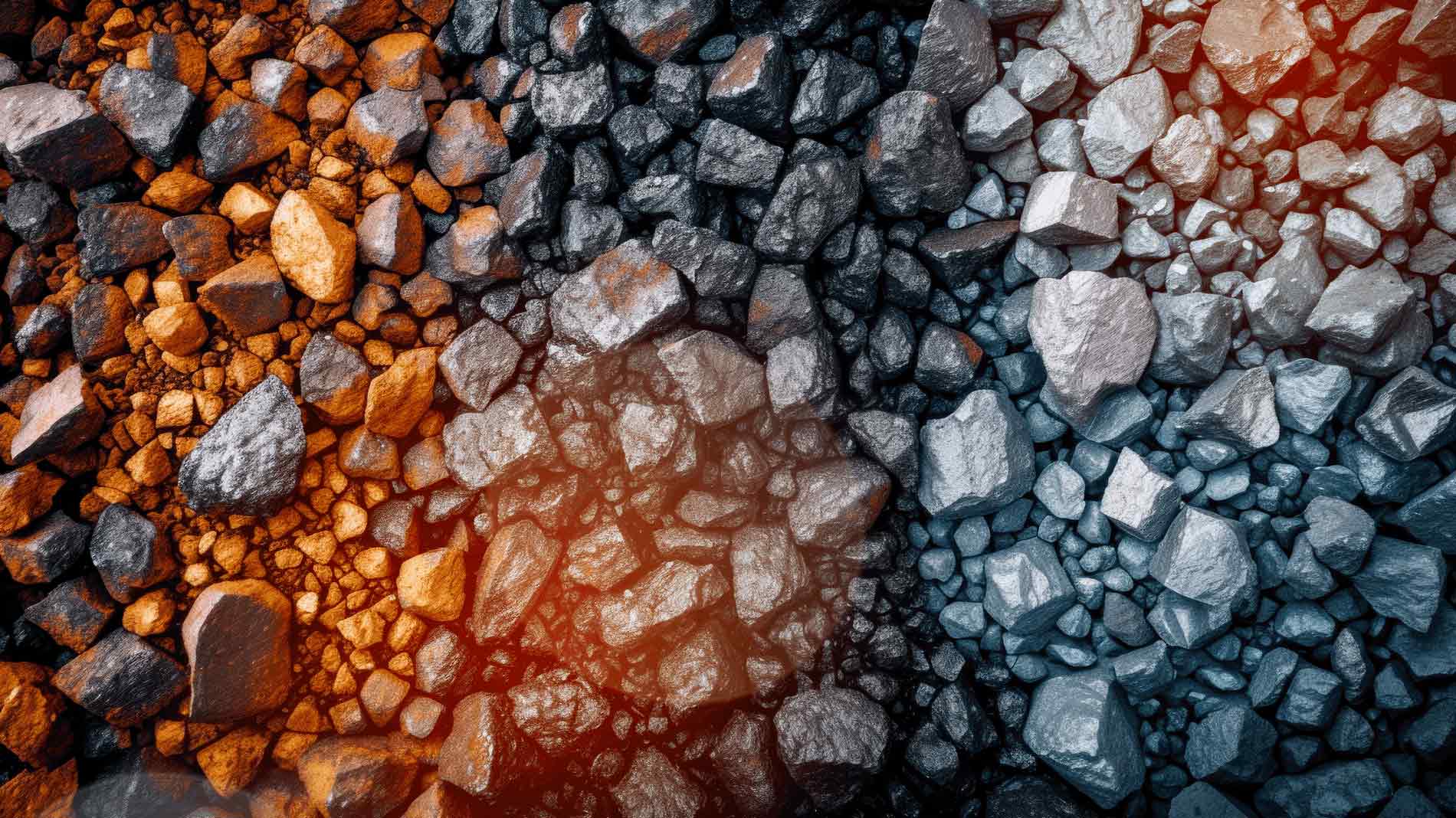
Raw Materials
Each battery cell necessitates a unique blend of specialized raw materials to ensure its functionality and suitability for its intended application. These materials encompass rare earth elements, lithium, manganese, and cobalt, which are either mined from hard rock or extracted from underground saline water deposits. Using specific chemicals, these materials undergo dissolution and precipitation processes to be extracted and purified. Subsequently, they are processed into the various components of a battery cell during the following production stages.
More on this topic